Diecast cars! We love ’em, we collect ’em, and we admire their tiny, detailed perfection. But have you ever stopped to think about how these little metal marvels actually come to life? It’s a surprisingly intricate process, involving skilled designers, complex machinery, and a whole lot of passion. So, buckle up, and let’s take a look behind the scenes of diecast car production.
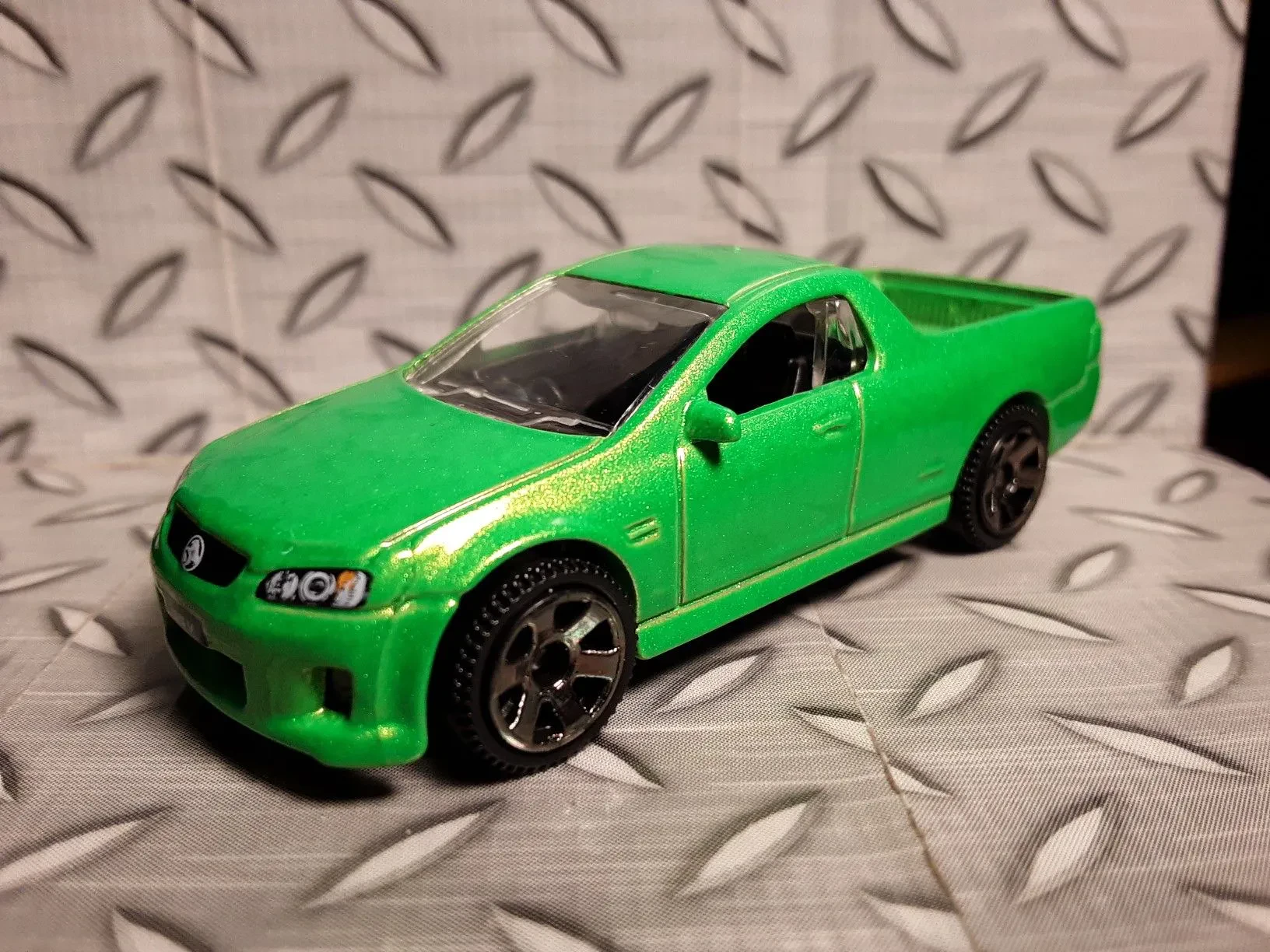
From Idea to Blueprint The Design Phase
It all starts with an idea, often based on a real-life vehicle. The design team gets to work, meticulously researching the car’s specifications, dimensions, and unique features. This involves pouring over blueprints, photographs, and sometimes even getting their hands on the real thing!
Using sophisticated CAD (Computer-Aided Design) software, the designers create a 3D model of the car. This digital blueprint is incredibly detailed, capturing every curve, contour, and crevice of the original vehicle. They even consider things like where the screws will go and how the car will be assembled.
The design phase also involves choosing the scale of the diecast car. Common scales include 1:18, 1:24, 1:43, and 1:64, each offering a different level of detail and size. The chosen scale will influence the entire manufacturing process.
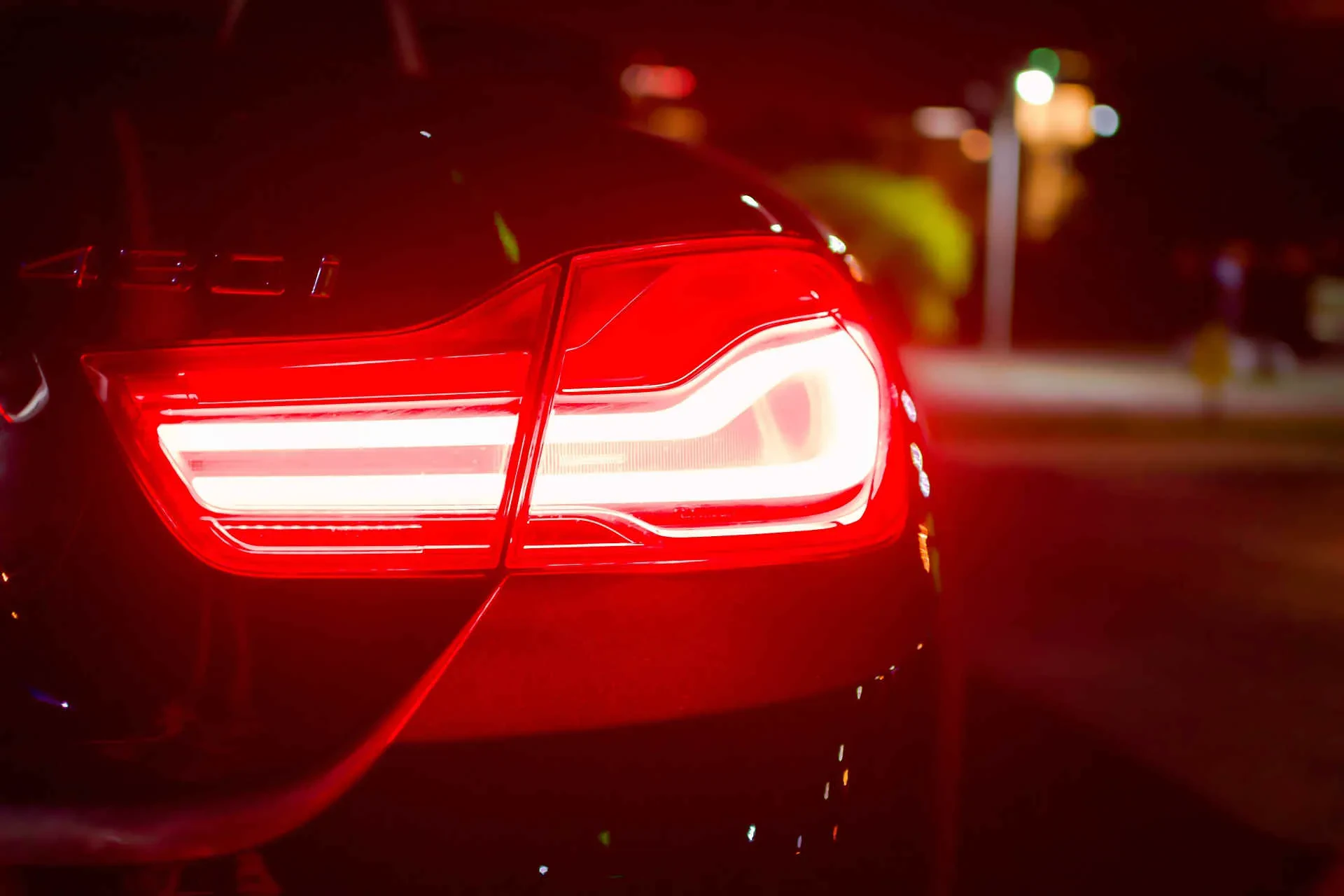
Creating the Molds The Heart of Diecasting
Once the design is finalized, it’s time to create the molds. These molds are the heart of the diecasting process, essentially negative spaces that molten metal will be injected into to form the car’s body. They’re typically made from hardened steel and require extreme precision.
The 3D model is used to create a master pattern, which is then used to machine the molds. This is a highly skilled process, often involving CNC (Computer Numerical Control) milling machines. The molds are created in multiple parts to allow for the removal of the diecast car after it solidifies.
The mold cavities are meticulously polished to ensure a smooth surface on the finished diecast car. Any imperfections in the mold will be transferred to the final product, so attention to detail is crucial.
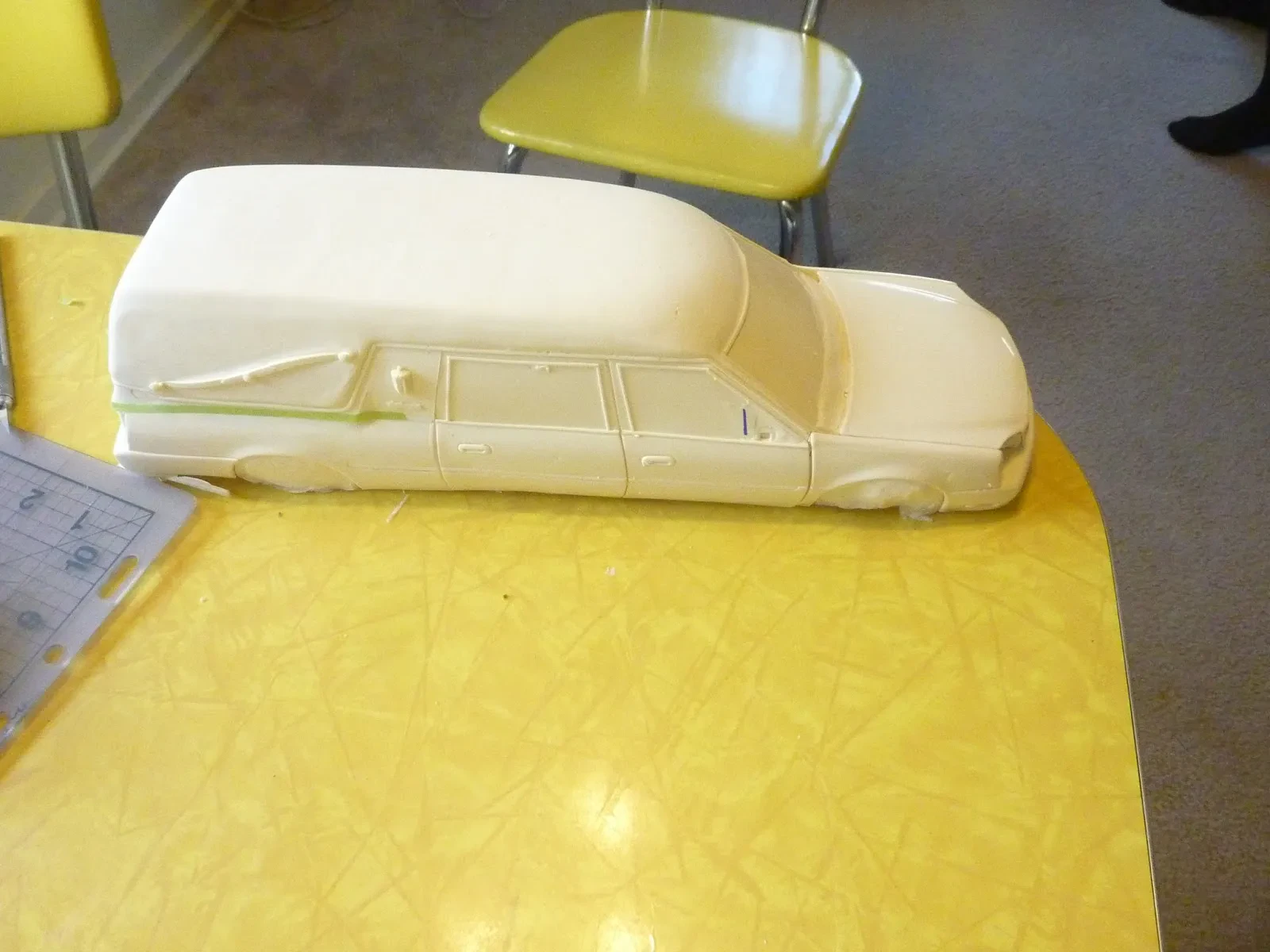
The Diecasting Process The Molten Metal Magic
Now comes the fun part the actual diecasting! This is where molten metal is injected into the molds under high pressure. The metal used is typically a zinc alloy (often called zamak or mazak), which is chosen for its strength, durability, and ability to hold fine detail.
The molds are clamped together tightly, and molten metal is forced into the cavity. The metal cools and solidifies rapidly, taking the shape of the mold. Once the metal has cooled sufficiently, the mold is opened, and the newly formed diecast car body is ejected.
This process is incredibly fast, with some machines capable of producing hundreds of parts per hour. However, it requires precise control of temperature, pressure, and timing to ensure consistent quality.
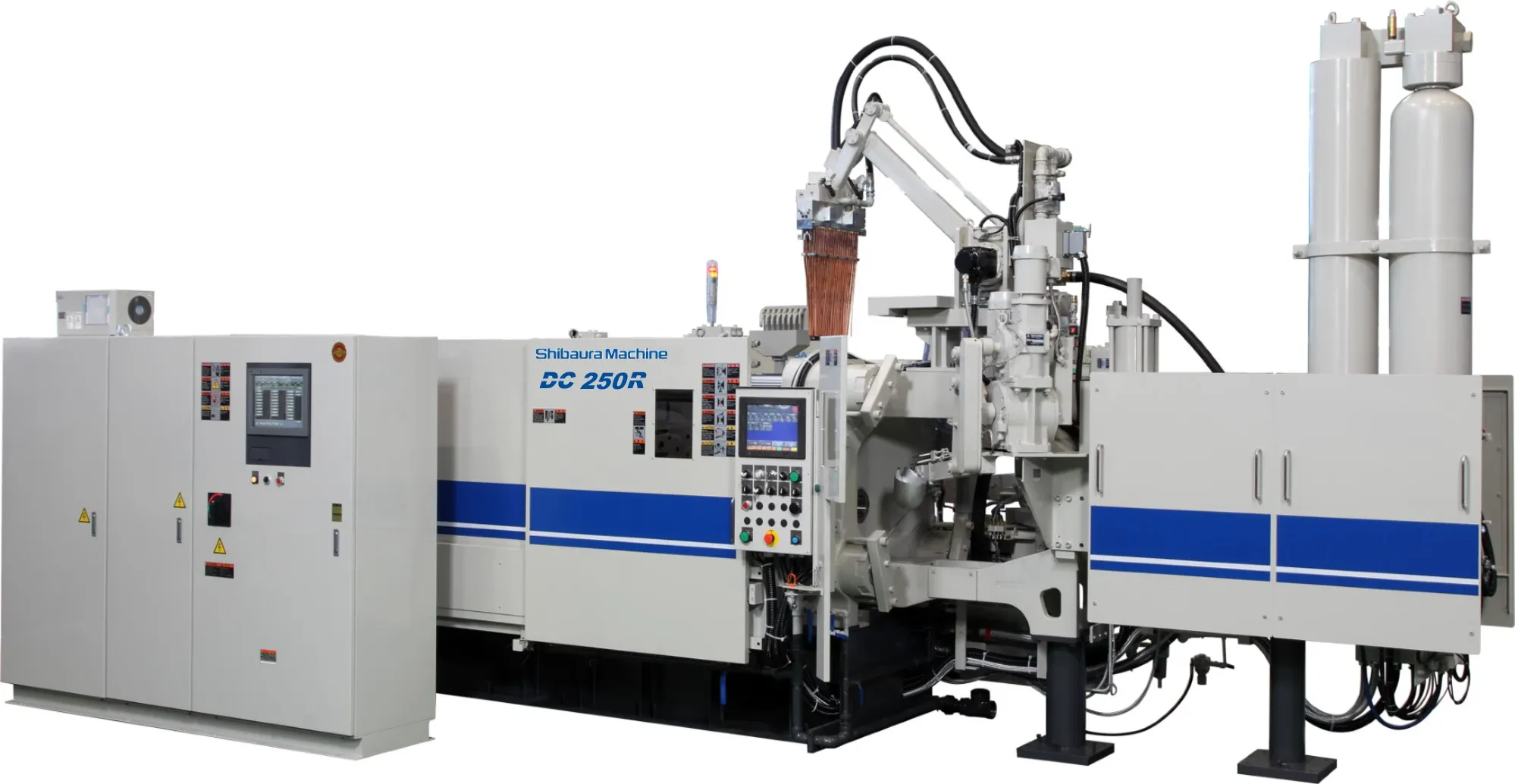
Cleaning, Painting, and Detailing Bringing the Car to Life
The raw diecast car body is far from finished. It needs to be cleaned to remove any imperfections or residue from the casting process. This often involves tumbling the parts in a special media to smooth the surfaces.
Next comes the painting. The car body is typically coated with a primer to ensure good adhesion of the paint. Then, multiple coats of paint are applied, often using automated spray painting systems to ensure even coverage.
After painting, the car body is decorated with tampo printing, which is a process similar to screen printing but used for curved surfaces. This allows for the application of intricate details like logos, stripes, and other markings.
Finally, the car is assembled. This involves attaching the wheels, axles, interior details, windows, and other components. Many of these parts are made from plastic or rubber and are often manufactured separately.
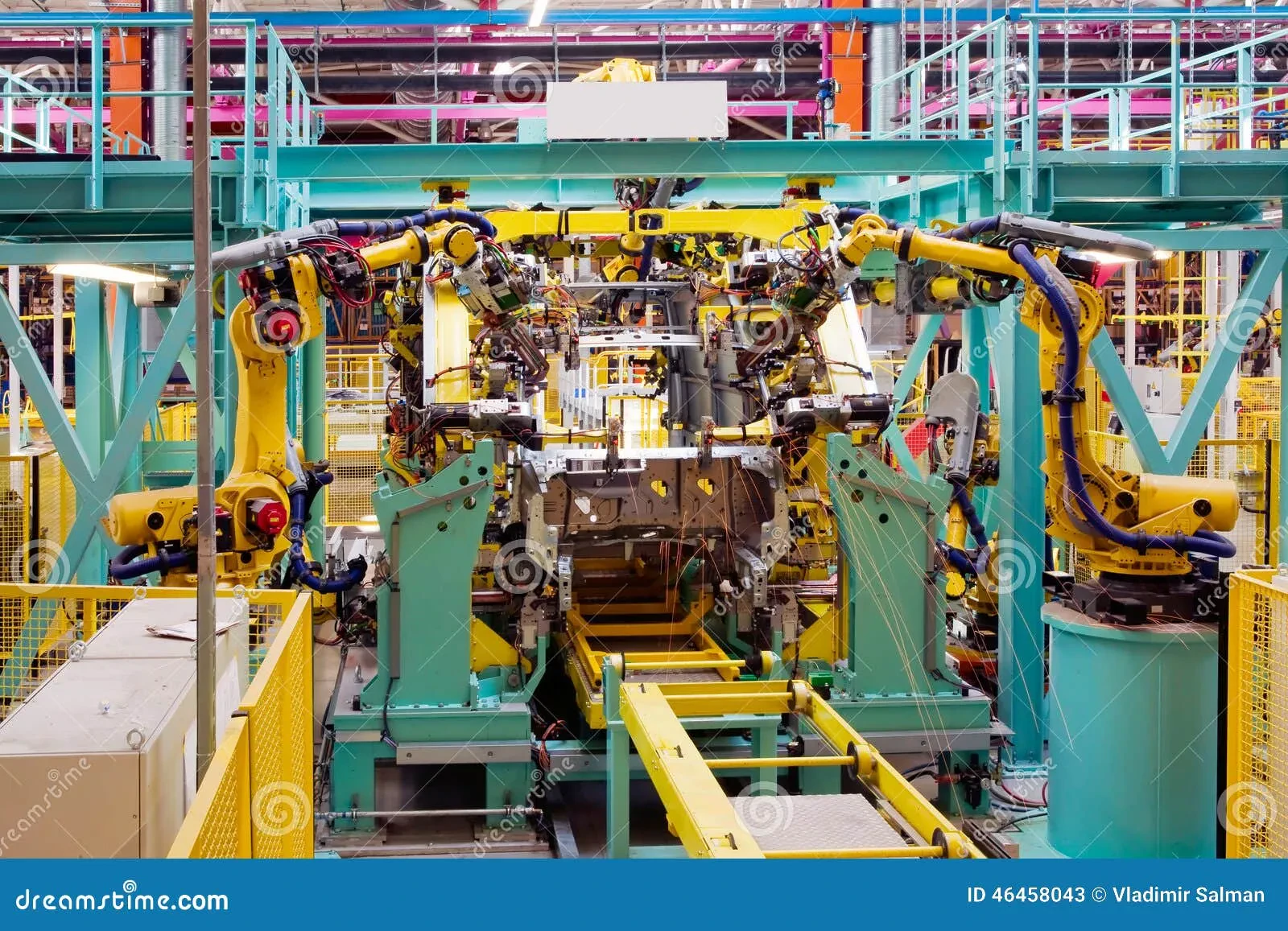
Quality Control Ensuring Perfection
Throughout the entire manufacturing process, quality control is paramount. Each stage is carefully monitored to ensure that the finished product meets the required standards. This includes checking for defects in the casting, painting, and assembly.
Diecast cars are often subjected to rigorous testing to ensure their durability and safety. This may involve dropping the cars from a certain height, exposing them to extreme temperatures, or testing the strength of the wheels and axles.
Only those cars that pass all the quality control checks are deemed fit for sale. The others are either reworked or scrapped. This commitment to quality is what makes diecast cars such prized collectibles.
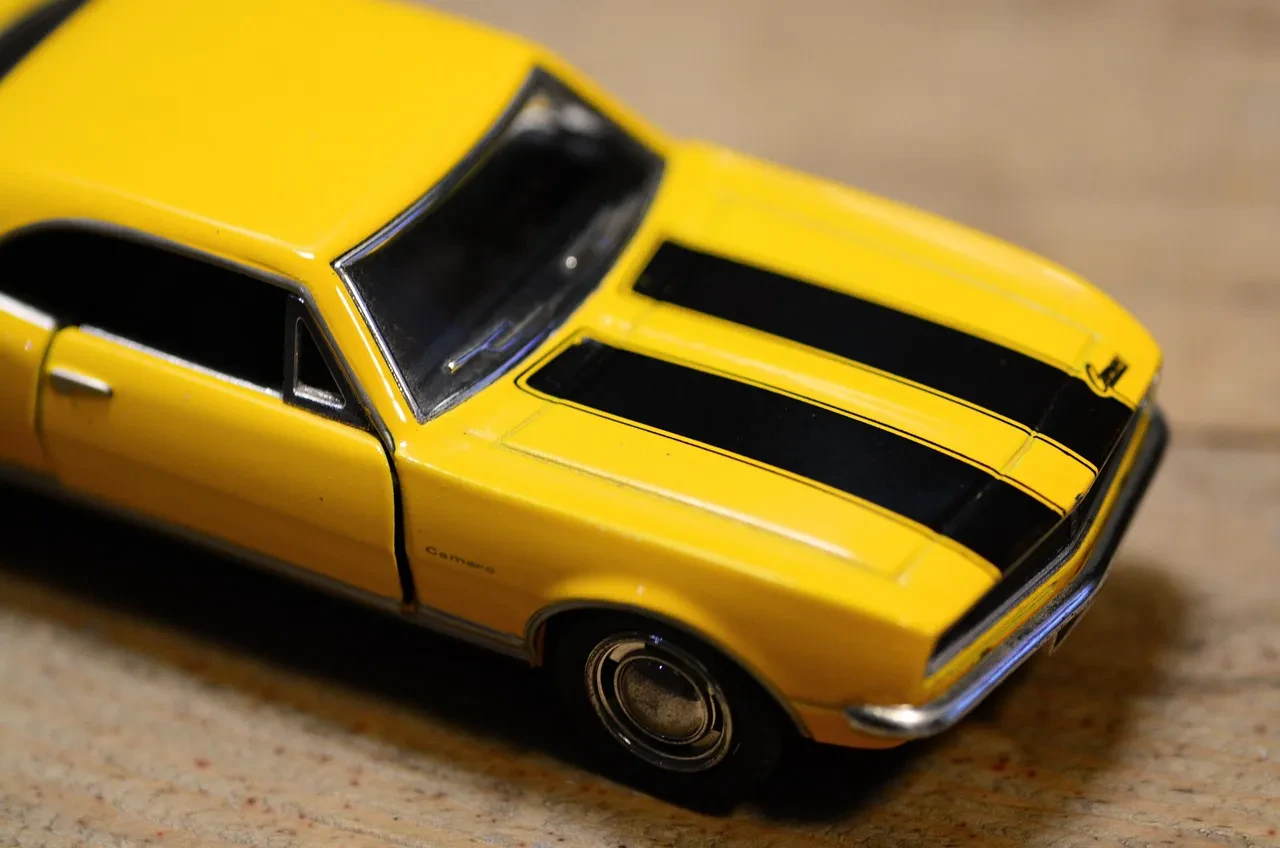
Packaging and Distribution Ready for the World
Once the diecast cars have passed quality control, they’re carefully packaged to protect them during shipping. The packaging often includes a clear plastic window so collectors can admire the car without opening the box.
The packaged cars are then distributed to retailers around the world. This may involve shipping them by sea, air, or land, depending on the destination. And finally, they arrive on the shelves of your favorite toy store or hobby shop, ready to be added to your collection.
So, the next time you pick up a diecast car, take a moment to appreciate the incredible effort and craftsmanship that went into its creation. From the initial design to the final packaging, it’s a complex and fascinating process that brings miniature automotive dreams to life!
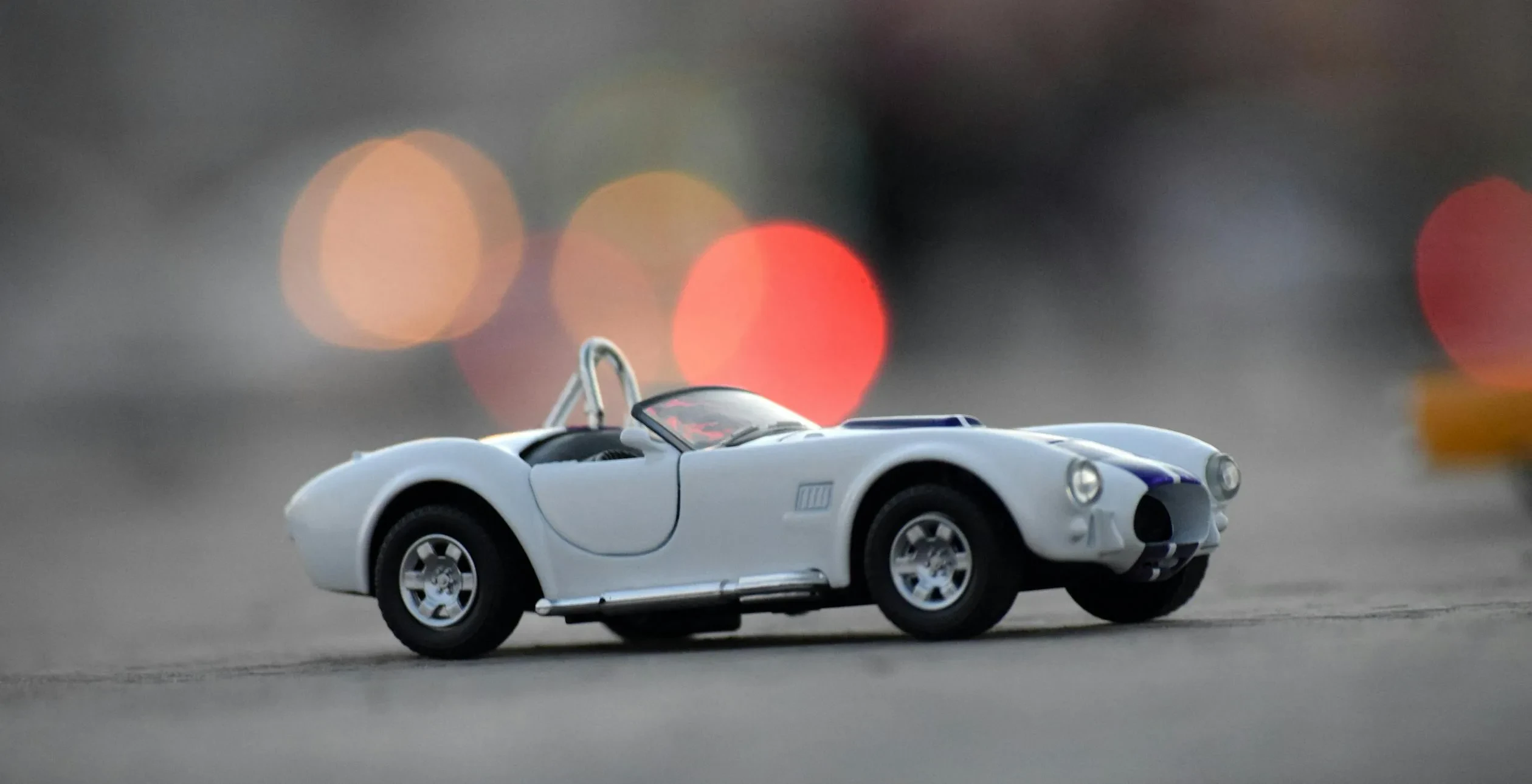
The world of diecast car production is constantly evolving, with new technologies and techniques being developed all the time. From more detailed models to more sustainable manufacturing processes, the future of diecast cars looks bright. Happy collecting in 2024!