Alright, let’s talk about mold flow analysis in the world of die casting. If you’re new to this, don’t worry, we’ll break it down so it’s easy to understand. Basically, mold flow analysis is like a virtual test run for your die casting process. It uses computer simulations to predict how molten metal will flow into the die, solidify, and ultimately affect the quality of your final part. Think of it as a crystal ball, letting you see potential problems before they actually happen.
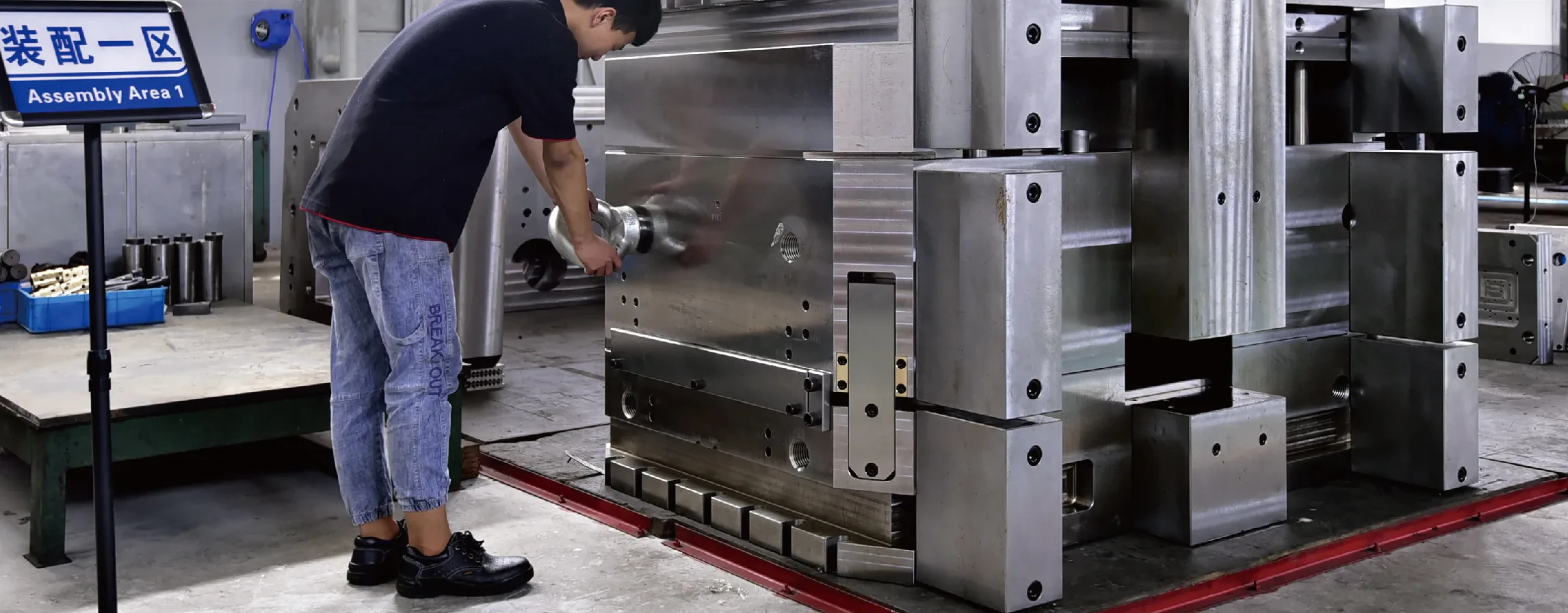
What Exactly is Mold Flow Analysis?
Imagine you’re designing a complex die casting part. You’ve got all the dimensions, the material chosen, and a plan for how the metal will be injected. But how do you know if that plan will actually work? Will the metal fill all the cavities properly? Will there be areas that cool too quickly, causing defects? That’s where mold flow analysis comes in.
Mold flow analysis uses sophisticated software to simulate the entire die casting process. It takes into account factors like the shape of the mold, the properties of the molten metal (like aluminum, zinc, or magnesium), the injection pressure, the temperature of the die, and even the cooling system. The software then crunches all those numbers and provides a visual representation of how the metal will behave.
It’s not just a pretty picture, though. Mold flow analysis provides valuable data about potential problems like air entrapment (leading to porosity), weld lines (where two streams of metal meet), incomplete filling, and hot spots that can cause distortion during cooling. By identifying these issues early on, you can tweak your design and process to avoid costly mistakes later.
The Steps Involved in Mold Flow Analysis
While the exact steps might vary depending on the software and the complexity of the part, here’s a general overview of how mold flow analysis works:
- CAD Model Preparation: The first step is to create a 3D CAD model of the die casting part and the mold itself. This model needs to be accurate and detailed to provide reliable simulation results.
- Meshing: The CAD model is then divided into a mesh of smaller elements. The finer the mesh, the more accurate the simulation, but also the more computationally intensive it becomes.
- Material Properties Definition: You need to tell the software what material you’re using and its properties at different temperatures. This includes things like viscosity, thermal conductivity, and specific heat.
- Process Parameter Setup: Next, you define the parameters of the die casting process, such as the injection pressure, metal temperature, die temperature, and cooling system parameters.
- Simulation: The software runs the simulation, calculating how the molten metal will flow through the mold and solidify. This can take anywhere from a few minutes to several hours, depending on the complexity of the part.
- Analysis of Results: Once the simulation is complete, you analyze the results. This involves looking for potential problems like air traps, weld lines, incomplete filling, and hot spots. You can also see how the temperature and pressure change throughout the process.
- Optimization: Based on the analysis, you can make changes to the mold design, the process parameters, or even the material. You then run the simulation again to see if the changes have improved the results. This process is repeated until you achieve an optimal design and process.
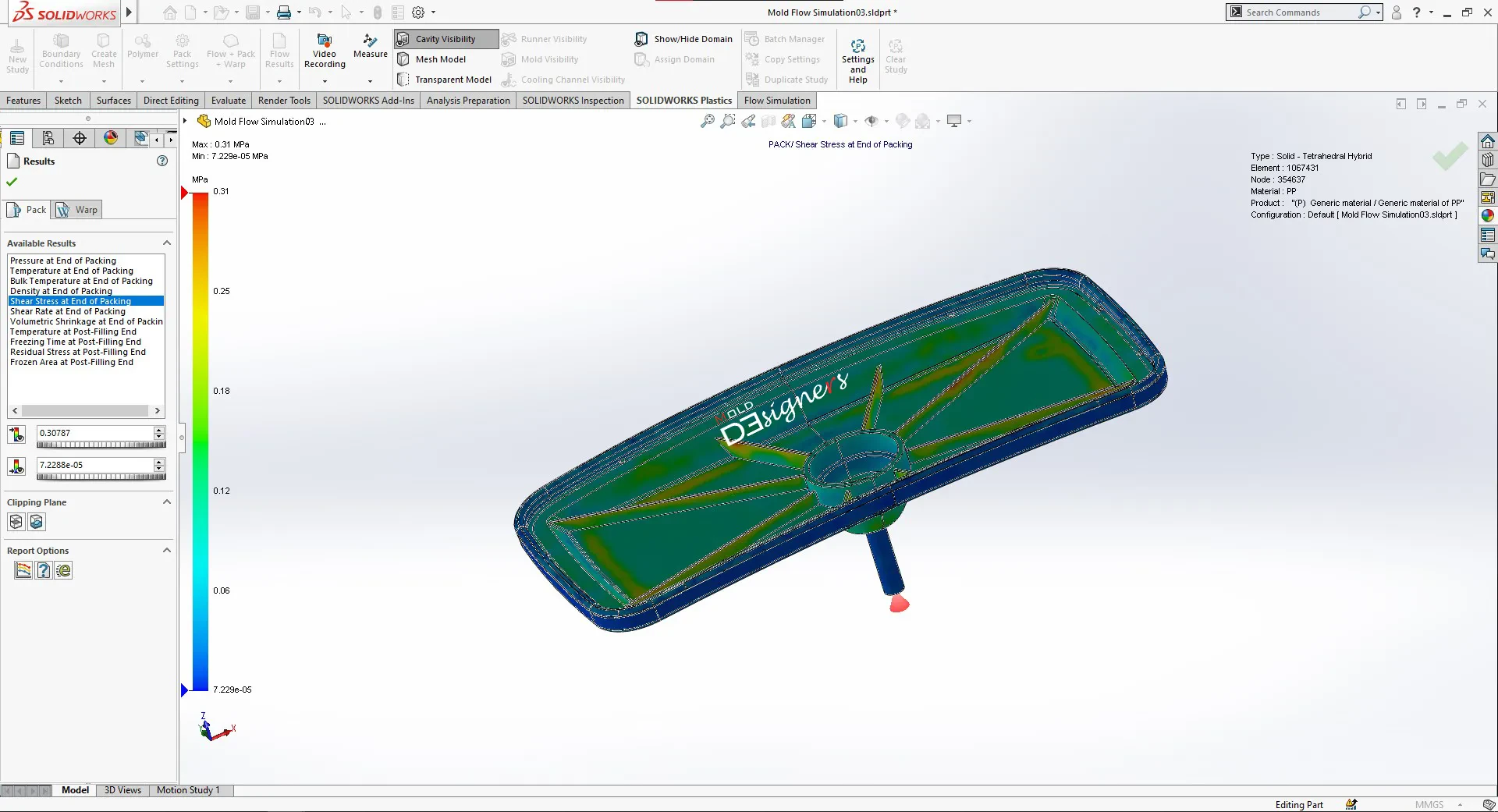
Why is Mold Flow Analysis So Important for Die Casting?
Okay, so why should you even bother with mold flow analysis? Here’s the deal: it can save you a ton of time, money, and headaches in the long run. Here’s how:
- Reduced Tooling Costs: Modifying a die after it’s been built is incredibly expensive and time-consuming. Mold flow analysis helps you identify potential problems early on, so you can make changes to the design before the die is even created.
- Improved Part Quality: By optimizing the mold design and process parameters, you can ensure that the metal fills the mold properly, minimizing defects like porosity, weld lines, and incomplete filling. This leads to higher quality parts that meet your specifications.
- Shorter Cycle Times: Mold flow analysis can help you optimize the cooling system, reducing the time it takes for the metal to solidify. This can significantly reduce cycle times, increasing production throughput.
- Reduced Scrap Rates: By identifying and eliminating potential problems, you can reduce the number of rejected parts, minimizing scrap rates and saving money on materials.
- Faster Time to Market: By identifying and resolving potential issues early in the design process, you can avoid delays and get your product to market faster.
- Better Understanding of the Process: Mold flow analysis provides valuable insights into the complex dynamics of the die casting process. This can help you better understand how different factors affect the quality of the parts, allowing you to make more informed decisions.
Benefits in 2024 and Beyond
In 2024, the benefits of mold flow analysis are even more pronounced. With increasing demands for complex, high-precision die castings, and the push for sustainable manufacturing, using mold flow analysis is not just a good idea; it’s often essential. By optimizing material usage and reducing scrap, it directly contributes to a more sustainable and cost-effective production process.
Furthermore, advancements in simulation software continue to enhance the accuracy and speed of mold flow analysis. Cloud-based solutions and AI-powered optimization tools are becoming more common, making the technology more accessible and user-friendly for even smaller die casting operations. This means more businesses can now leverage the power of simulation to improve their processes and stay competitive.
Who Uses Mold Flow Analysis?
Mold flow analysis is used by a wide range of people involved in the die casting process, including:
- Design Engineers: Use it to optimize the design of the die casting part and the mold.
- Manufacturing Engineers: Use it to optimize the die casting process parameters.
- Tooling Engineers: Use it to design and build the mold.
- Quality Engineers: Use it to ensure that the parts meet the required specifications.
- Project Managers: Use it to manage the die casting project and ensure that it stays on schedule and within budget.
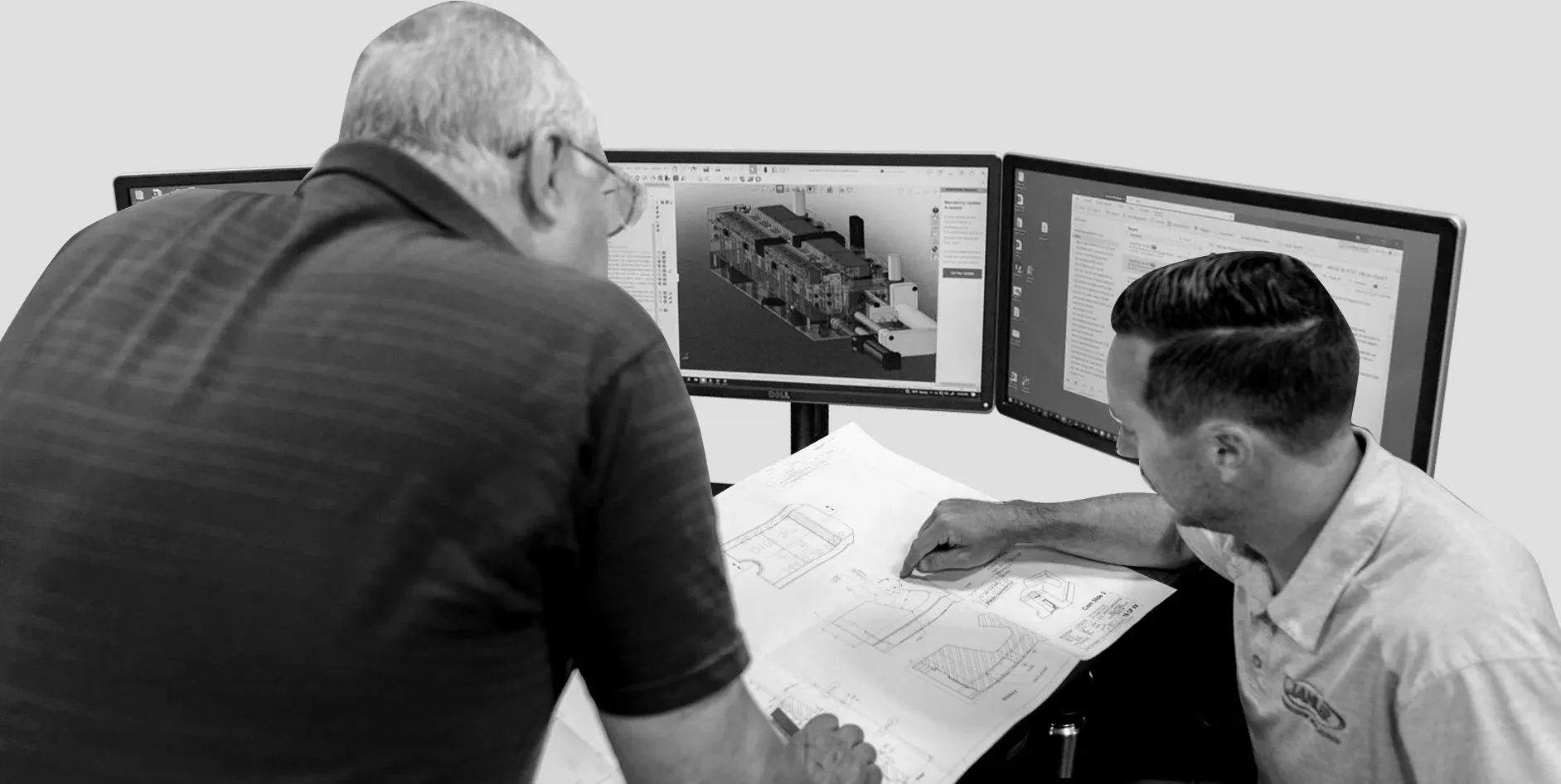
What to Look for in Mold Flow Analysis Software
If you’re considering investing in mold flow analysis software, here are a few things to keep in mind:
- Accuracy: The software should be able to accurately simulate the die casting process and predict potential problems.
- Ease of Use: The software should be easy to learn and use, with a user-friendly interface.
- Features: The software should have all the features you need to analyze and optimize your die casting process, such as the ability to simulate different materials, processes, and cooling systems.
- Support: The software vendor should provide good technical support.
- Cost: The software should be affordable for your budget.
There are many different mold flow analysis software packages available, so it’s important to do your research and choose the one that best meets your needs.
In a Nutshell
Mold flow analysis is a powerful tool that can help you improve the quality, efficiency, and profitability of your die casting operation. By simulating the die casting process, you can identify potential problems early on and make changes to the design and process to avoid costly mistakes. If you’re not already using mold flow analysis, it’s definitely something to consider.
Investing in mold flow analysis might seem like an upfront cost, but think of it as an investment in the long-term success of your die casting business. The savings on tooling costs, improved part quality, shorter cycle times, and reduced scrap rates will quickly pay for itself.
So, there you have it – mold flow analysis in die casting explained in plain language. Hopefully, this has demystified the process and given you a better understanding of its importance. Now go forth and cast with confidence!