We all love the gleam of a perfectly crafted diecast car. But have you ever stopped to think about the journey it takes to get from a factory machine to your eager hands? It’s a fascinating process that involves numerous stages of quality control, ensuring that the model you buy matches the manufacturer’s high standards (or at least, it should!).
The Stages of Diecast Quality Control
Quality control in diecast manufacturing isn’t a single step; it’s a multi-stage process that happens throughout the production line. Think of it as a series of checkpoints, each designed to catch potential flaws before they make it onto your shelf.
1. Raw Material Inspection
It all begins with the raw materials. The metal used for the body, the plastic for the interiors – everything is carefully inspected for imperfections. This includes checking for consistent thickness, proper composition and freedom from defects.
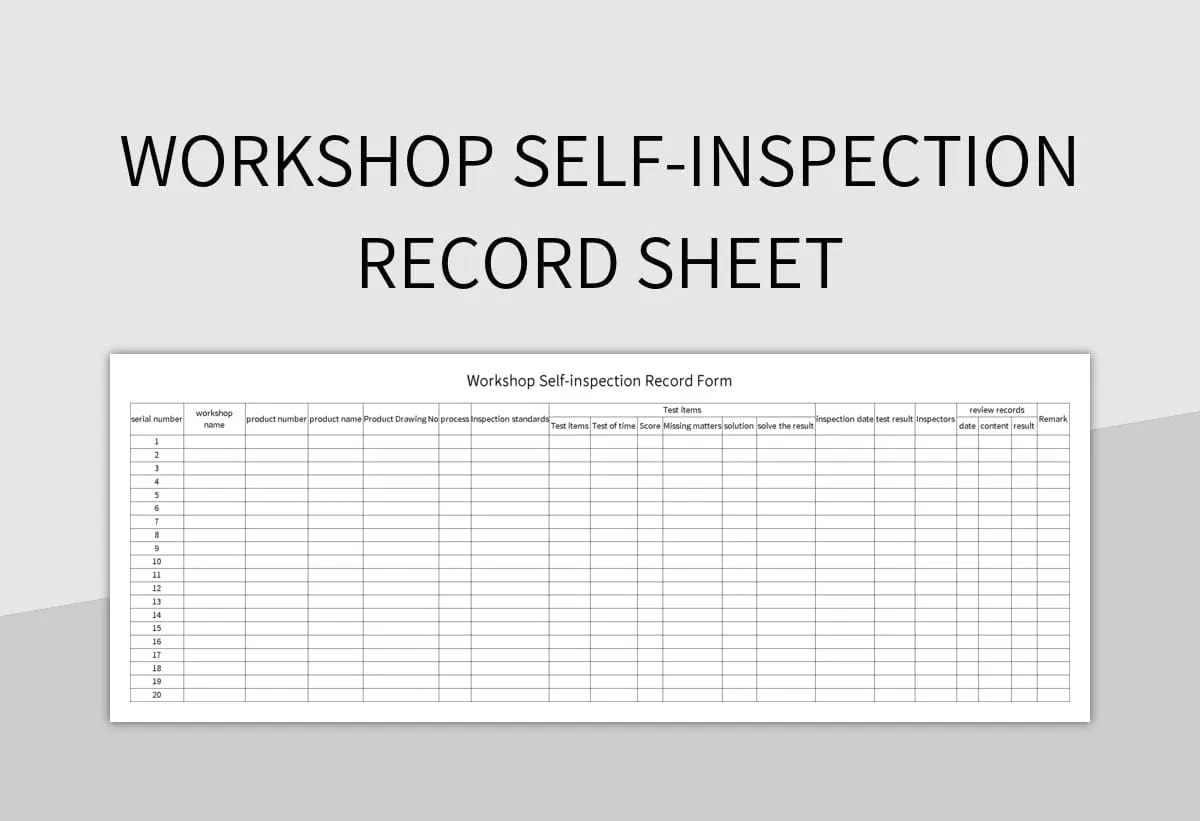
2. During the Casting Process
The casting process itself is closely monitored. Machines are regularly calibrated to ensure consistent metal flow and proper mold filling. Any defects in the casting, such as air bubbles or incomplete fills, are immediately flagged.
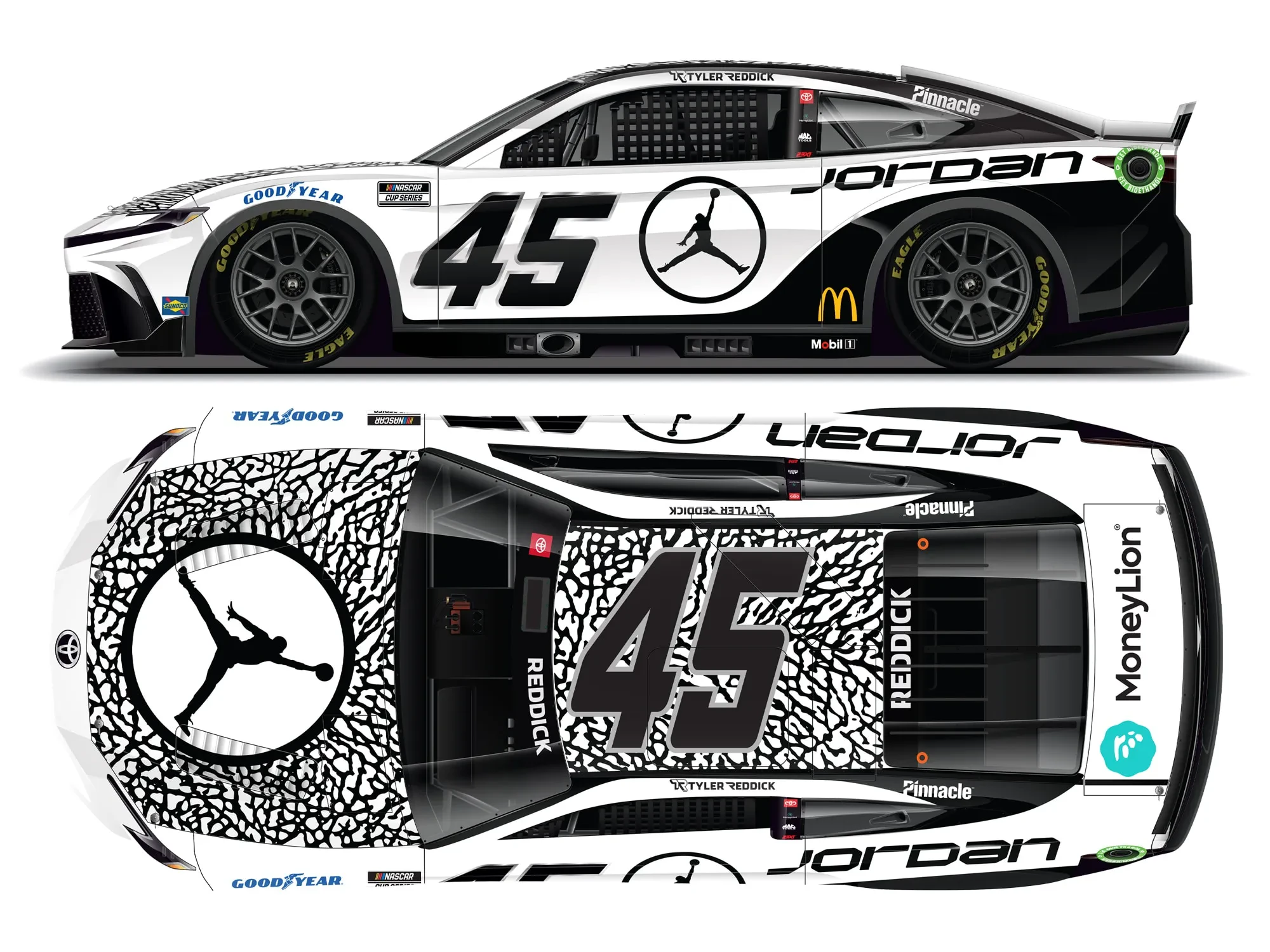
3. Post-Casting Inspection
Once the diecast body is cast, it undergoes a thorough visual inspection. This is where many flaws are identified. Workers carefully check for flash (excess metal), warping, scratches, or other surface imperfections. Often, this is a combination of automated systems and human eyes, each with its own strengths.
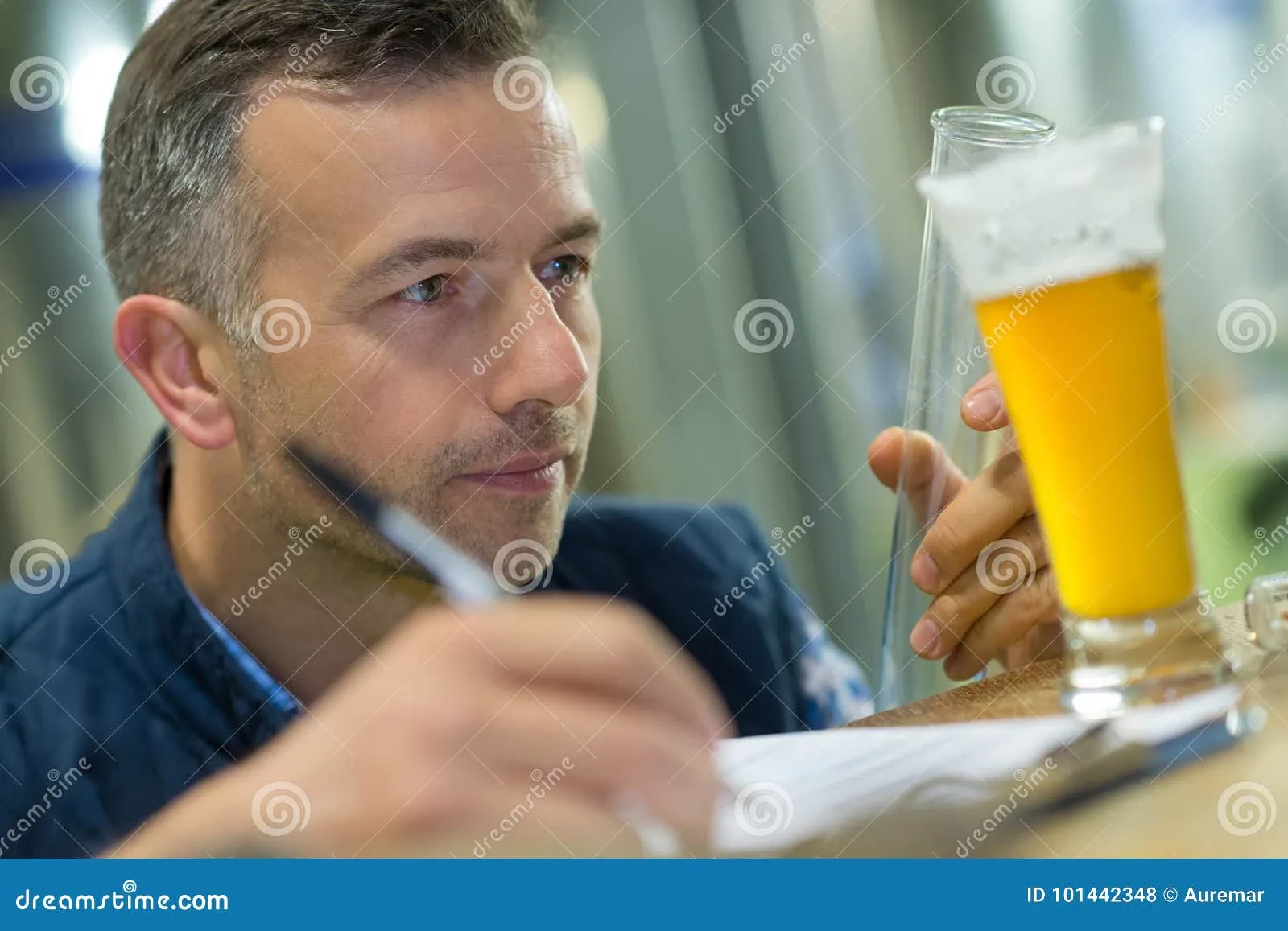
4. Painting and Decoration
The painting process is another critical stage. The paint must be applied evenly, and any imperfections in the application, such as runs or drips, are noted. Decals and tampo printing also receive close scrutiny to ensure they’re correctly aligned and sharp.
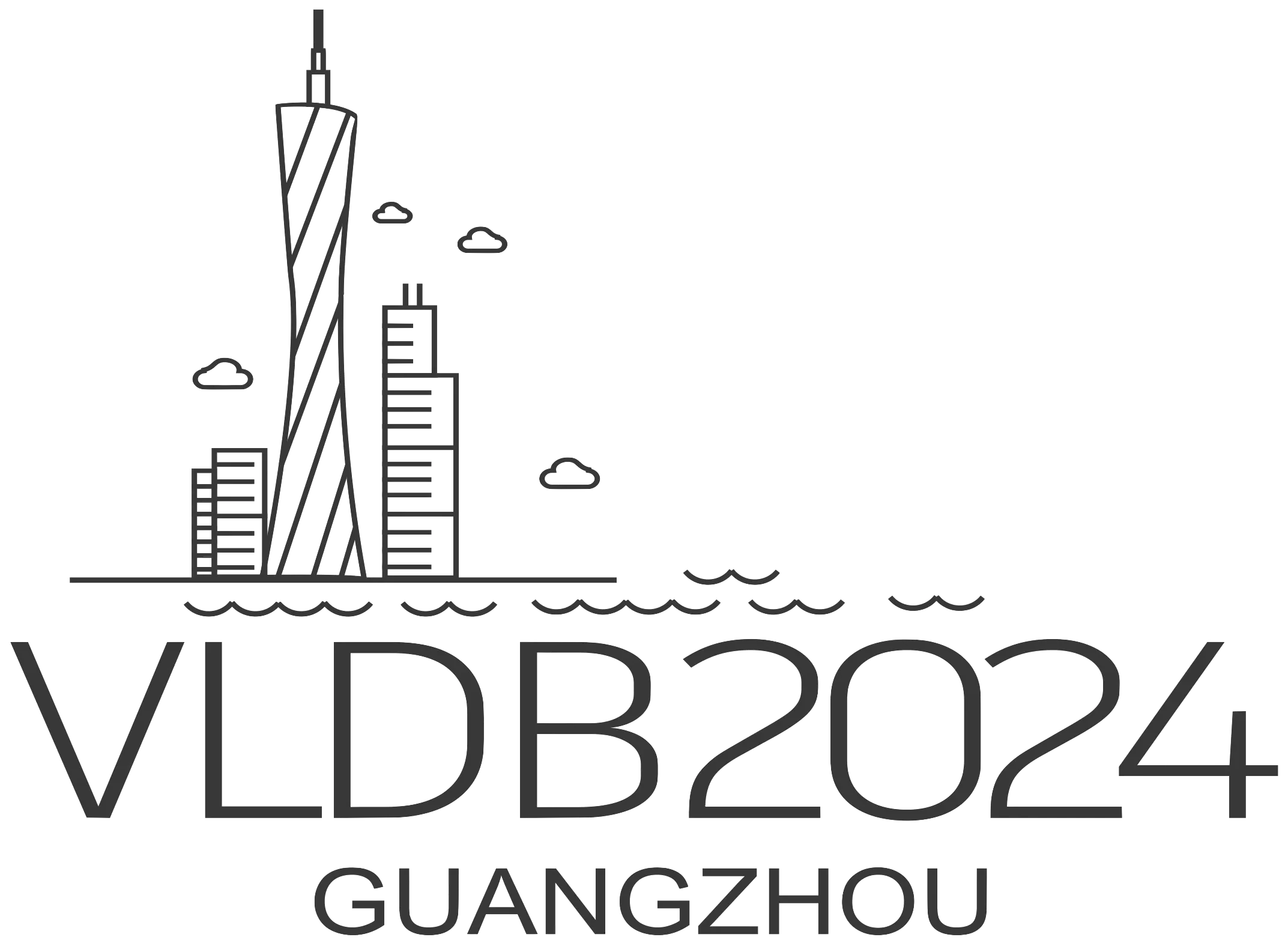
5. Assembly and Final Inspection
Finally, the various components of the model are assembled. This is where the wheels, chassis, and interior are added. A final inspection ensures everything fits properly, the paint is intact, and the overall model meets the specified quality standards. This often includes a check for loose parts or misalignments.
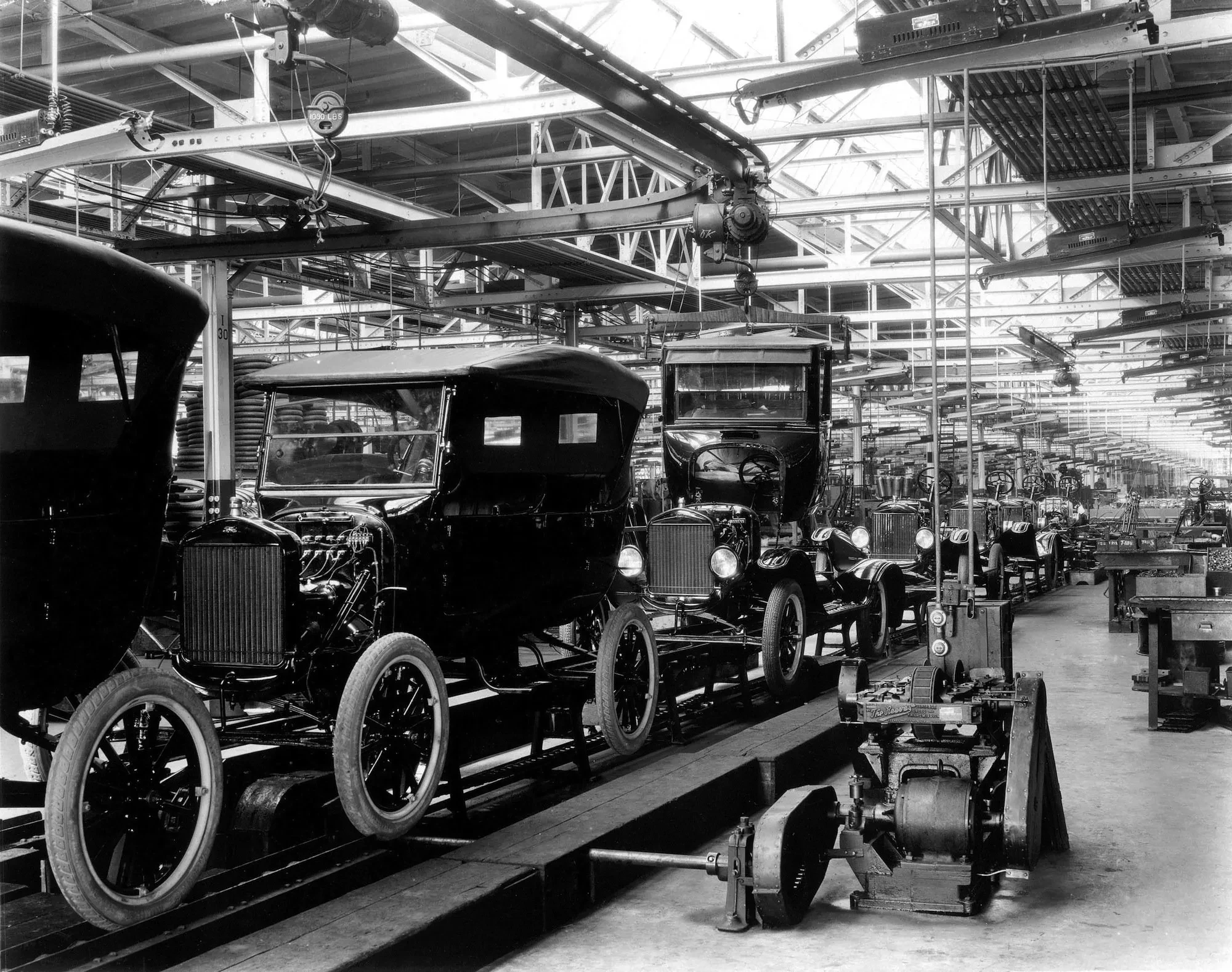
6. Packaging and Shipping
Even after the model passes inspection, quality control continues. The packaging is checked for damage, and the models are carefully packed to prevent damage during shipping. This final step ensures the pristine condition when it reaches collectors.
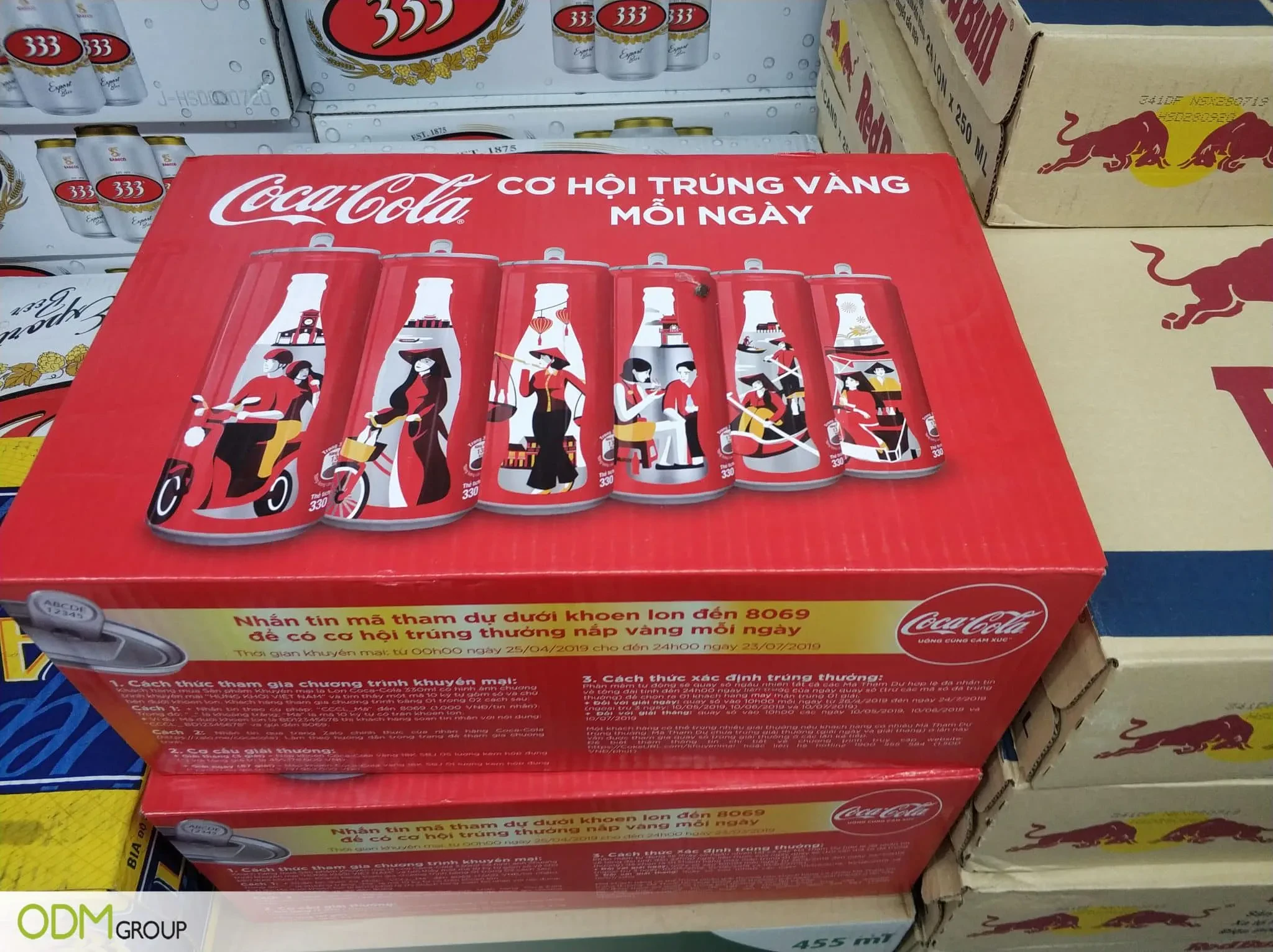
What to Look For in a High-Quality Diecast
- Sharp, clean details
- Even paint application
- No visible flaws or blemishes
- Properly aligned decals
- Solid construction with no loose parts
- Detailed interior and exterior features
- Correctly functioning features (if applicable, like opening doors or hoods)
While no diecast is completely perfect, these are the hallmarks of a high-quality model that has undergone rigorous quality control. Paying attention to these details will help you appreciate the craftsmanship that goes into creating these miniature marvels.